Front Page
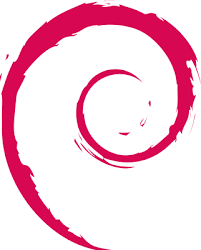
Remount eines eingehangenen Mountpoints
Aktuell konfiguriere ich auf einem Raspberry rum. Dort ist das root Verzeichnis natürlich readonly eingehangen.Wie aber kann man einfach, zur Laufzeit neu mounten? Auf dem Linux system sieht es wie folgt aus (Eingabe mount) Also einfach nur folgendes eingeben: mount –rw /dev/mmcblk0p2 / erzeugt eine Meldung: mount: /: /dev/mmcblk0p2 already mounted on /. so gehts …
Ein neues Großmodell muss her – Losi DBXL
Im Sommer war ich mit einingen Modellbau-Kollegen in einem Tagebau etwas bashen. Dort war ebenfalls ein Fahrer mit seinem DBXL 2.0 e. Es passiert ja nicht oft, aber diesmal habe ich mich auf Anhieb verliebt 🙂 Er fuhr eine 12 S Kombo, von ZTW. Sehr cool. Nach zahlreichen Wochen des Überlegen und zauderns, kam dann …
Bashvariablen
Gelegentlich muss ich ein paar Skripte schreiben. Nach zahlreichen Monaten vergesse ich aber immer wieder wie das Variablen Handling mit der Bash ist. Und zur Gedächtnisstütze dient dieser Artikel. $0 – Name des Skriptes ( wie in C) $1 – $9 – Die ersten 9 Parameter die dem Skript übergeben wurde $# – Anzahl der …
Bash prüft ob ein Verzeichnis existiert
Möchte man in einem Shellscript prüfen ob ein Verzeichnis existiert oder nicht, kann man das mit folgendem Code erledigen. den negierten Fall kann man wie folgt abbilden